DECARBONIZING WITH DIGITAL: IMPROVING DRILLING AND WELL CONSTRUCTION PERFORMANCE, SUSTAINABLY
As the world emerges from the pandemic, oil demand that was slashed by corona virus-related lockdowns and travel restrictions is once again on the uptick. While demand forecasts are being updated continuously to account for the dynamic situation with the virus, current indicators point toward oil reaching pre-pandemic levels by the end of 2022, followed by a period of continued growth. This is setting the stage for a multi-year, demand-led recovery for the industry.
To fill an anticipated supply gap, oil producers are gearing up to drill and complete new wells, but they face a much different energy landscape than even just a few years ago. Today, climate change has brought the industry’s very license to operate under scrutiny. Global stakeholders want more visibility into the activities, risks and opportunities of the oil and gas sector. The industry is responding through sustainability reporting to demonstrate its climate-related impact and actions to reduce CO2 emissions. In tandem, a more volatile and risk-averse market environment is causing operators to exert far more discipline over their spending.
One of the drivers behind this is an expected reduction in market share for hydrocarbons over the next several decades, as more renewable forms of energy come online. Even so, hydrocarbons will have a significant role to play as a reliable energy source in the total energy mix, to meet projected global demand growth. The confluence of these and many other factors has resulted in industry mandates for more sustainable drilling and well construction operations, and higher levels of efficiency and performance to increase margins, drive free cash flow, and minimize environmental impact.
Aligning digital with decarbonization. For many years, digital has been key for operators to achieve returns-focused performance, but today it must go hand in hand with decarbonization, which is crucial to protecting the industry’s license to operate across every stage of the well life cycle. In the drilling and well construction domain, this translates to reducing emissions per foot drilled, among other sustainability actions, such as reducing power consumption and optimizing the well footprint.
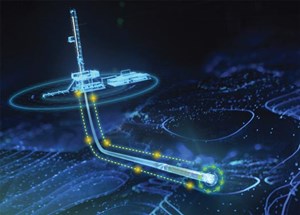
Digital solutions—including open, cloud-based platforms and applications, digitally connected technologies, edge computing and intelligent systems—present some of the industry’s best opportunities to realize performance gains and reduce emissions, Fig. 1. But with climate change impacts continuing to mount, digital alone is not enough. Today’s digital transformation efforts must align with strategic decarbonization planning that is both target-driven and transparent. This achieves two things for the industry: it drives a convergence of digital and sustainability, and builds a greater sense of trust at a societal level that is crucial to the industry’s future. Schlumberger recently announced its decarbonization plan, committing to net-zero greenhouse gas (GHG) emissions by 2050. As part of this commitment, Schlumberger has aligned with the Task Force on Climate-related Financial Disclosures (TCFD) and Sustainability Accounting Boards (SASB) to ensure transparency along its net-zero journey and third-party validation of its progress.
The company’s plan includes a comprehensive, near-term, emission reduction roadmap and interim targets for its Scope 1, 2 and 3 emissions. Scope 3 emission sources include emissions both upstream and downstream of an organization’s activities. For Schlumberger, this encompasses its customers’ operational Scope 1 and 2 emissions, which account for 75% of the company’s baseline GHG footprint.
Schlumberger has set an aggressive reduction target of 30% for its Scope 3 emissions by 2030. In support of this, the company recently introduced its Transition Technologies* portfolio that aims to reduce CO2 emissions while simultaneously driving efficiency, reliability and performance gains. To quantify the impact of the technologies and solutions in this portfolio, many of which are enabled by digital, the company has developed a robust quantification framework aligned to eight attributes, including emissions reduction, energy consumption reduction and electrification, that support the United Nations’ Sustainability Development Goals. The framework enables benchmarking through net footprint comparisons of various technologies, drives the qualification process for incorporating new technologies into the portfolio, and informs the most optimal impact-reducing choices for the customer.
In addition, Schlumberger has started embedding sustainability into its digital enablers. An example of this is the company’s work to incorporate sustainability metrics into its digital applications for well planning and delivery. These applications will, in coming years, include new functionality to help operators do everything from select the most impact-reducing cement to the most efficient rotary steerable system (RSS) for a given operation.
As digital and sustainability become more closely intertwined, the industry will continue making significant strides with digital to minimize carbon footprint through advanced, remote operational capabilities, optimized drilling and well construction workflows, and improved directional drilling performance and efficiency. As edge-enabled hardware and intelligent learning technologies continue to evolve, the industry is also working toward a fully autonomous bottomhole assembly (BHA), and later, fully orchestrated autonomous well construction. The latter will help operators achieve significantly higher levels of efficiency and performance beyond what is currently achievable.
Connecting people, applications and data. When it comes to achieving step changes in performance and efficiency with digital, one of the most significant challenges that the industry faces today is connecting people, applications and data. The need for this becomes very apparent when looking at well planning and construction workflows. Large volumes of data are required for everything from planning the trajectory of the well to determining the cement slurry blends. Very often, however, these data are underutilized, because it’s not readily accessible to stakeholders at the right time and in the context of their role. In addition, operators’ internal teams, vendors or suppliers are not always aligned, and working collaboratively, at every stage of well planning and execution. Other challenges include a lack of consistency for drilling wells, which is crucial for achieving more sustainable performance.
Open, cloud-based environments that combine domain science with advanced digital technologies are critical to enabling operators to unlock the full value of their data. Open applications in these environments provide key opportunities for operators to transform their well planning and construction activities to significantly improve their consistency, safety and efficiency.
Fundamentally, open cloud-based applications enable easier access to the right data and information; more collaborative engagement; and greater opportunities to leverage automation and data analysis. During the well planning stage, a key benefit of such applications is that they can facilitate a single, constantly updated version of the well plan that can be accessed by everyone at each stage of the process. They also can leverage data from offset wells to automatically generate the best sequence of operational activities, thus improving planning efficiency. When available, features such as automated trajectory design and automated engineering analysis can reduce manual tasks that free up engineering time for more complex tasks. This not only optimizes well planning workflows but also has a significant impact on improving field-wide well performance through greater engineering innovation.
Today, open and modular applications that leverage drilling domain knowledge, and advanced machine learning (ML) and artificial intelligence (AI) solutions, can execute a digital drilling plan consistently and automate drilling tasks. Open environments and applications allow drilling contractors, operators and software vendors to build and deploy their own proprietary capabilities, further enhancing efficiency and control during the well construction process.
Building new alliances. To achieve even higher levels of performance, technology partnerships and collaborations with other industry service providers are key. In 2019, Schlumberger and Dataiku announced an exclusive technology partnership to enable the E&P industry to build and deploy its own AI solutions across the full breadth of their upstream workflows within the open DELFI* cognitive E&P environment. Dataiku is a centralized data platform that democratizes the use of data science, ML and AI in the enterprise. In the drilling and well construction domain, this platform has enabled Schlumberger to test its ideas to advance the effectiveness of its well planning and delivery applications, as well as enabling its customers to enhance their own workflows when using the cognitive E&P environment.
In 2020, Schlumberger and OMV Upstream announced an enterprise-wide deployment of AI and digital solutions enabled by the cognitive E&P environment, across OMV’s global operations. Schlumberger’s well planning application helped plan eight wells in the time that it would normally take to plan one. This has helped OMV to achieve a 40% reduction on planning time.
Schlumberger also recently announced its collaboration with NOV to combine the automated capabilities of Schlumberger’s well delivery application with NOV’s rig automation platform. This will help accelerate customers’ adoption of drilling automation technologies, enabling superior well construction performance.
Advancing remote operations. In the industry’s journey toward operations with more sustainable performance, a key element has been to transition its people to working remotely. For decades, supervisory control and data acquisition (SCADA) systems have enabled real-time field activity monitoring and operational support services. Today, this operating model is now widely used across the industry. While there are still many benefits to this model, there are also drawbacks, such as requiring service company engineers at the rig site to perform a wide variety of tasks.
Over the years, as digital technologies and infrastructure have evolved, so too has the service model for remote operations. Today, the industry has seen a shift from real-time monitoring to live remote operations control. What this means is that service company engineers can now perform their mission-critical tasks from offices in town rather than at the rig site, reducing carbon emissions from personnel logistics, on-site housing and equipment transportation.
The pandemic really brought the need for such a service model to the forefront. At the onset of the pandemic, removing people at the rig site was imperative for health and safety purposes, but so, too, was operational continuity. This new model enabled both. But even before the pandemic, the industry was already beginning to recognize a need for improved performance through centralization. To realize performance gains, the service industry needed a way to consolidate and enhance executional decisions by connecting a smaller number of engineer decision-makers to a wider network of data and domain expertise.
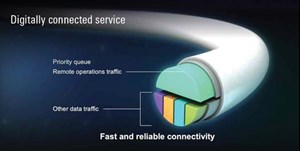
Schlumberger’s answer to this is its digitally connected service, which enables remote work capabilities for engineers by providing them with instant access to data and multi-domain experts via robust digital network linking centers spanning the globe, Fig. 2. The technology infrastructure behind this service includes strategically placed servers in certain countries to reduce data latency and ensure compliance to local data residency regulations. Schlumberger also provides dedicated quality of service allocation for all remote operations on its network and those of its customers, which eliminates connection reliability issues for all remote operations tasks.
During the pandemic in 2020, more than 65% of Schlumberger’s jobs worldwide used the service, in more than 84 countries, and drilled more than 6,500 sections, which accounted for more than 27,000,000 ft drilled and logged while averting 6,900 personnel trips—all with zero health, safety and environmental (HSE) incidents. In the Midland basin, Oxy and Schlumberger teams collaborated to achieve a new drilling milestone using the digitally connected service, drilling 9,506 ft in a 24-hr period. The drilling of this lateral section set a new company-wide 24-hr footage record for any section, and reflects a step change in performance, eclipsing the previous record by more than 20% while keeping the entire lateral in the target zone. This achievement was accomplished safely through cooperation across customer development, asset and operations teams, and Schlumberger drilling and remote operations experts.
The journey toward autonomy. The next performance leap for efficiency and sustainability in the well construction domain is autonomy. Unlike automated systems, technology and processes, which replace some manual tasks performed during the well construction process, fully autonomous systems eliminate virtually all manual tasks, enabling more efficient, consistent and sustainable operations. Much like the auto industry’s endeavor to build and deploy autonomous vehicles, the industry has been on a similar journey in the well construction domain. What the industry is working toward is a fully autonomous BHA drilling every section of a well: a system that can constantly analyze its position, formation characteristics, conditions, and trajectory to optimize steering and well placement.
While many of the building blocks of autonomy already exist today, including digitally connected technologies and hardware, edge intelligence, and live remote operations control capabilities, the industry is still several years away from delivering a fully autonomous solution for well construction—but it’s making significant inroads.

The industry’s journey toward autonomy, and increased system cognition, can be aligned to six successive degrees, Fig. 3. The baseline is defined by full human control and no automation, and the final step is fully autonomous systems. Today, the industry is deploying systems capable of performing single-workflow autonomy, where self-regulating systems autonomously prioritize and respond to simultaneous events. The next step in the journey is to reach orchestrated autonomy, where the system can prioritize multiple workflows, integrating intelligent planning and execution with automation at the wellsite, from the surface to downhole. This is what the industry is advancing toward and where significant opportunities exist to increase drilling and completion performance.
Many of the technologies in development today have single workflow autonomy. Schlumberger recently introduced Autonomous Directional Drilling, which includes solutions to steer autonomously through any section of the wellbore. This enables the BHA to react to data in real time, while also reducing surface interference and minimizing downlinks from surface to the downhole RSS, resulting in the drilling of more accurate wells, faster.
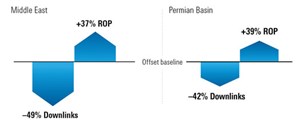
In the Middle East, an operator used autonomous downhole control system capabilities with an RSS to drill curves on four wells. The combined solution enabled the operator to reduce downlinks to the RSS 49%, as compared to offset wells drilled in manual mode, while achieving a 37% increase in rate of penetration (ROP), Fig. 4. In the Permian basin, an operator used a similar solution to drill the curve and lateral sections for seven wells autonomously. The operator reduced downlinks by 42% per 100 ft drilled for all curves, while also increasing ROP by 39%, compared with similar intervals drilled in the manual mode for offsets.
Autonomous systems represent the future of the industry and the crucial link between digital and sustainability. What the industry sees now is how autonomous systems can bring a step change to efficiency and performance for today’s operations—minimizing operational impact. As autonomy grows across more drilling and well construction workflows, enabled by advanced remote operations technologies, it will further support the industry’s efforts to achieve more sustainable performance by improving efficiency and minimizing the overall carbon footprint of operations. Further to this, open environments and applications will continue to unlock the value of data and optimize workflows to enhance efficiencies at every stage of well planning and operations. This will be done through enhanced collaboration, automation and data analysis capabilities.
The industry has an imperative to address climate change while contributing a reliable energy source to the energy mix for years to come. By aligning decarbonization and digital and staying focused on performance gains through leveraging transformative digital solutions, this is all within reach.