INNOVATIVE RSS DESIGN INCREASING EFFICIENCY OF DRILLING MORE COMPLEX WELLBORE PROFILES
The oil and gas wells of today present more complexities. Drilling often challenges operators with wells that have higher pressures, temperatures, and step-outs, as they attempt to maximize existing reservoir production and exploit deeper reservoirs. These wells may have complex designs and deeper depths through troublesome formations, which can result in nonproductive time (NPT) and exceeding the well authorizations for expenditure (AFEs).
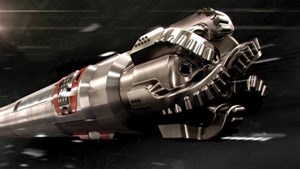
Historically, the oilfield industry has solved drilling challenges and technical limits through core technology improvements. The pursuit of drilling longer, deeper and faster wells at the turn of the millennium led to many advances in drilling technology, including the invention of the rotary steerable system (RSS). Now, increasing capabilities, drilling a quality borehole and optimizing the well construction process often demand this technology, at a minimum.
Rather than simply using the same approach time and again for the same results, complex wells require unconventional thinking and innovative solutions. Unconventional thinking is complemented by the paradigm of working in tandem with operators to resolve concerns and improve performance. Doing things differently enables drilling with higher efficiency and achieving new benchmarks in challenging applications. Strategies that push performance boundaries involve following a proven drilling engineering process, leveraging digitalization and automation solutions, incorporating offset well analyses, and creating a comprehensive drilling plan and contingencies, based on a risk assessment.
Weatherford uses this kind of approach to consistently deliver quality directional drilling. Several case studies from multiple countries in different regions throughout the world illustrate tangible performance improvements, from onshore land wells in Canada and Mexico, to deep offshore wells in the Black and North Seas. Accomplishments include increasing on-bottom rates of penetration (ROPs), drilling longer step-outs, using fewer bottomhole assemblies, finishing ahead of AFE, intersecting all planned targets, and even setting field records for ROPs, lateral lengths, and footage drilled.
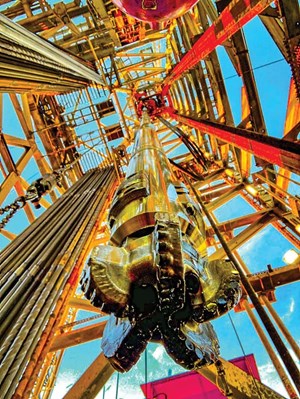
RSS built to solve operators’ challenges. In 2018, Weatherford launched a push-the-bit technology, the Magnus rotary steerable system, which represented a fundamentally different approach from those used in the past, Fig. 1. Weatherford purposefully engineered the RSS to reflect the market’s current needs for longer horizontals, faster drilling, more power to transmit, and more demands on wellbore quality.
The simple, cost-effective design improved asset utilization, compared with its predecessors, to reflect the economics of the existing market. As a reliable technology that enables drilling ahead while maintaining directional control, the RSS led to a rapid adoption curve. The Magnus RSS portfolio covers a broad scope of applications, with five different collar sizes from 4¾-in. to 11-in. and capabilities in borehole sizes from 57/8-in. to 18¼-in.
Each Magnus RSS in the portfolio features innovations in steering and power to address well requirements, such as smoother wellbores and longer laterals. A unique differentiator—three independently controlled pads—offers not only control of each of three pads to push the bit laterally, but also built-in redundancy for continued drilling in the unlikely event of actuator failure. One or all mechanisms can be turned off to drill a smooth curve and a less tortuous well at a planned dogleg. With all the pads de-activated, operators can safely trip in and out of the hole, drill out of casing, ream, and log with a completely passive steering head.
Aside from steering, the RSS also delivers capabilities to handle the anticipated torque and speed from current and future developments in drive technology. It eliminates non-rotating parts for a slick design that minimizes the risk of stuck-pipe events, saves on the expense of a highly stressed driveshaft, and uses the full diameter of the tool body to transmit torque to the drill bit.
Extending the RSS portfolio to slim hole sizes. After the success of the larger system sizes, Weatherford rolled out the slim-hole, 4¾-in. design tool, the Magnus 475 system, in 2020 with an equally aggressive field test and development strategy. Scaling the RSS designs up proved to be very efficient exercises, which allowed for vast cross-utilization of existing electronics and mechanical components. The RSS system used the 6¾-in. sized system as a basis but proved quite a bit more complicated, with almost all components requiring a scale-down and re-design. The main challenge consisted of fitting three independent valve and motor assemblies into the small 4¾-in. OD collar. At the same time, keeping the independent pad controller as a key differentiating feature was imperative to setting the RSS apart from existing push-the-bit technology on the market and affirming its position as the industry’s first fully rotating RSS to offer proportional steering control.