BREAKTHROUGH IN DIRECTIONAL DRILLING
Driven by the need to modernize in response to the increasingly challenging energy needs of the world, the oil and gas industry has witnessed several revolutionary technology transformations in recent decades. One such technology that found its roots in the need to quickly drill relief wells in the 1930s, directional drilling grew more efficient in the 1970s through the introduction of positive displacement motors. While this technology introduction was considered a step change at that time, it pales in comparison to the paradigm shift that resulted from the pursuit of drilling longer, deeper, and faster wells at the turn of the millennium—the introduction of rotary steerable systems (RSS).
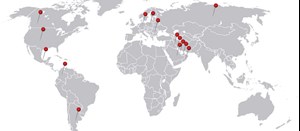
In its quest to supply hydrocarbons to fuel the world’s economy, the oil and gas industry faces multiple challenges: delivering wells that meet complex geo-mechanical requirements, on time and under budget, while complying with stringent regulations and addressing security and environmental considerations, to name a few. These challenges also create opportunities that are best addressed by an ecosystem of cutting-edge technology, supported by holistic engineering processes, operational excellence and competent personnel, who thoroughly understand the customers’ needs and reservoir challenges.
Weatherford’s first RSS offering, introduced in the early 2000s, was based on the “point-the-bit” concept, and saw several evolutionary design changes and sizes over the following decade in response to customer requirements. Then, in 2018, Weatherford launched a disruptive generation of “push-the-bit” RSS design—Magnus. A rapid adoption curve ensued, with Magnus commercially deployed in 15 countries and in five different collar sizes, ranging from 4 ¾ in. to 11 in. across a broad range of applications.
This “push-the-bit” RSS offers seamless integration with the rest of Weatherford’s premium drilling solutions, to meet the operator’s directional drilling demands. For instance, this RSS can be coupled with a downhole positive displacement motor for greater rate of penetration (ROP), lower surface torque, and reduced torsional dysfunctions (such as stick-slip). This RSS also can be integrated with under-reamer equipment while drilling to meet the well architecture demands. In addition, the RSS and logging while drilling (LWD) technologies offer crucial real-time formation evaluation (FE) data for reservoir characterization, staying on the planned course, and maximizing pay-zone exposure. This allows the operator to complete the drilling of wells faster and produce more hydrocarbons for longer.
DELIVERING SOLUTIONS CONSISTENTLY
As of August 2020, the International Association of Directional Drilling (IADD) has estimated that there are 70 different RSS tools in the market from multiple companies. Of these, over 70% are classified as push-the-bit systems, exemplifying the popularity of this approach over other steerable technologies, such as mud motors and point-the-bit RSS.
The increasing complexity of oil and gas wells has elevated the importance of wellbore quality and tortuosity management, which necessitates borehole deviation with accurate and precise Dog-Leg Severities (DLS) on demand. This represents a challenge for many RSS designs, such as the ones based on the steerable motor, directional drilling concept, which cannot offer total control of their steering mechanisms at any given time and must alternate steering modes with neutral to achieve an average DLS across any given interval.
The Magnus push-the-bit design overcomes this challenge by utilizing three independently controlled steering pads that allow proportional control, thereby offering infinite resolution of its steering bias. The steering pads are activated by drilling fluid ported via three rotary valves—one for each pad—allowing the pads to be deactivated easily for casing shoe drill-outs or reaming/back-reaming operations.
Another major challenge for RSS designs is to ensure that all parts on the outside of the tool rotate to establish the tool’s reference and steer as required, avoiding the use of a non- or slow-rotating sleeve. RSS tools with full collar rotation are less prone to sticking, and potentially becoming lost in hole (such an event would trigger a major non-productive time event). Not only should the RSS design deliver the operator’s directional requirements with minimum risk, it also needs to allow maximum asset uptime and utilization for the service provider: it needs to be simple to use, repair, redress and re-deploy.
DRILLING ENGINEERING PROCESS
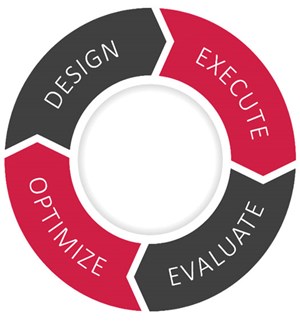
Design. This stage initiates the workflow by establishing and aligning the scope of work, project requirements and key performance indicators (KPIs). A risk assessment is conducted to identify and communicate all risks, as well as establish the control measures and contingency plans. Any deviations from this baseline plan are then assessed through the management-of-change (MOC) process.
Execution. The second stage of the process covers the execution of the drilling program, whereby the drilling engineering team monitors the services in real time (RT), to optimize drilling performance, and to identify and mitigate hazards. During this phase, digitalization and automation solutions are critical to gather, consolidate and process data from multiple sources, using built-in intelligence to expand the analytical capacity of the drilling engineers. Centro is one such platform, which allows faster and smarter decisions during the execution phase.
Evaluation. Once the directional drilling work is completed, the drilling engineer evaluates the service performance by benchmarking against previously established KPIs, documenting on-the-job knowledge gains, and customizing the end-of-well report, as required. The vendor’s workflow adds every job to the Centro database, making its dynamic models more robust and making it more valuable to the drilling engineering cycle.
Optimize. During this last phase, the service company’s drilling engineers study post-well analytics. They use Centro to establish further optimization solutions for implementation in future well designs, with the goal to improve drilling performance on a field-wide scale.
In summary, the service company’s approach to consistently deliver quality directional drilling solutions is based on three guiding pillars: novel RSS technology, robust drilling engineering quality process, and an agile digitalization and automation platform. This approach has been field-proven in multiple countries in different regions, and further discussion is presented through case histories from Mexico and the Middle East.
MEXICO LANDSCAPE
With over 450 oil fields, 130 of which are offshore, Mexico offers a broad range of drilling environments. While hydrocarbons are spread across ten main sedimentary basins, about 90% of all oil discoveries have been in the southern basin (which extends into the Bay of Campeche) and the rest are in the Tampico-Misantla-Veracruz basin. About 97% of oil production is from naturally fractured carbonate reservoirs in the Cretaceous and Jurassic ages, while Tertiary sandstones are primarily gas reservoirs. An offshore discovery in 2017 proved oil presence in an Upper Miocene sandstone and provided new insights for exploration in Mexico’s deepwater Gulf. Despite over a century of commercial oil production, it is estimated that over 90% of the country’s slice of the Gulf of Mexico (GOM) remains unexplored.
Mexico onshore: The first Magnus tool was deployed in May 2018; this entailed a Magnus 675 successfully drilling the 8 ½-in. S-shape well section in a single run. In doing so, Magnus replaced the planned steerable mud motor and achieved a 35% ROP increase, enabling the customer to safely reduce well construction time, facilitating smoother casing running by delivering lower tortuosity while staying within the allowable DLS limit of 2.5° / 100 ft (30 m).
Following this successful run, the Magnus technology was deployed in different configurations, in increasingly complex environments:
- Logging while drilling (LWD) tools to capture formation evaluation data
- Underreamer equipment added to improve the Equivalent Circulating Density (ECD) management across a tight drilling window
- Penetrating the harder Cretaceous prior to moving offshore
- Reducing BHA pick-up times by running the single RSS collar solution, which includes the measurement while drilling (MWD) tool.
Following the successful runs in these environments, the first Magnus 475 was run near Poza Rica, Veracruz, in August 2020. The key element for these successes was the integration of the drilling engineering quality processes and the Real Time Operation Center (RTOC) expertise with the operator’s drilling program. The success was facilitated further by collaboration with Weatherford Integrated Services and Projects (ISP), which helped the operator reduce interface risk and improve operational efficiency by using only one drilling services provider. As of Aug. 15, 2020, over 20 wells have been drilled onshore Mexico with Magnus, one of which is detailed below.
Magnus 950 onshore Mexico. In early 2020, after the operator saw multiple service quality events with another service company resulting in loss of wellbore position—center-to-center distance between the plan and actual surveys reached 52 ft (16 m)—Weatherford was called out to restore the borehole to plan and reach the 12 ¼-in. section total depth (TD) at about 21,300 ft (6,500 m). The plan required steering the well in 3D through the Eocene and Paleocene, dropping inclination by 3° while turning 15° in azimuth, and then holding a 22° tangent to TD. Additional considerations for designing the job were low ROP (extended time below rotary table, BRT); high mud weight of 16.5 ppg (1.98 SG); possibility of mud losses; presence of a reverse fault; and bottomhole circulating temperature (BHCT) close to 150° C.
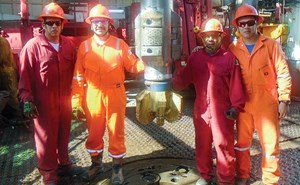
These best practices allowed the operator to successfully reach a final 12 ¼-in. section TD at about 22,000 ft (6,700 m) and were fully captured in Centro for optimizing future drilling operations.
Mexico offshore. Six months after the first Magnus job in Mexico, it was time to demonstrate its capabilities in the Gulf. In November 2018, Magnus successfully drilled the 8 ½-in. 3D curve, to land a well in the Jurassic interval at around 15,700 ft (4,800 m) under the Campeche Bay waters in a single run. In doing so, Magnus replaced a prominent RSS, which had been drilling in the area for several years. Coupled with the drilling engineering approach, the Magnus technology allowed the operator to exceed the expected average ROP of 30 ft/hr (9 m/hr) by about 80% and position the wellbore, as per plan, with a DLS under the maximum allowable value of 3.75° / 100 ft (30 m), thereby saving the operator 12 days in this section. This case of drilling a 3D curve in anhydrite illustrates just one of the many GOM drilling and geo-mechanical challenges.
Throughout the technology deployment in Mexico, several challenges were overcome through iterative technology improvement. These included shallow directional work with RSS to reach far-away targets; narrow drilling windows that required managed pressure drilling (MPD) integration; diverse lithology that could require directional drilling without returns (pumping seawater as sacrificial fluid in mud cap drilling); and coupling the RSS with Tungsten Carbide Insert (TCI) ) bits to drill Breccia intervals, geosteer in production intervals to maximize pay-zone exposure, and tight well architecture that requires borehole enlargement-while-drilling tools in the RSS BHA. As of Aug. 15, 2020, 18 wells have been drilled with Magnus offshore Mexico, one of which is detailed below.
Magnus 1100. At the end of 2019, an 11-in. Magnus RSS was selected to drill a directional 17 ½-in. section through the Pliocene and Upper Miocene intervals. In addition to the drilling performance metrics, the main challenge was to build the curve from about 10° up to 55° inclination across these soft formations, and this required maintaining enough pad force against the wellbore. The drilling engineering team created a comprehensive design, based on multiple BHA simulations to balance the natural BHA tendency, pad pressure requirement, and drill bit Hydraulic Horsepower per Square Inch (HSI) to maximize the DLS output. The BHA was able to deliver the curve and tangent with minimum bias setting, without exceeding the maximum DLS, and fulfilling the expected ROP. This allowed the operator to set and cement the 13 ⅜-in. casing per plan and continue drilling the rest of the well, Fig. 2.
DRILLING CHALLENGES IN THE MIDDLE EASTERN ARENA
The oil rich carbonate reservoirs of the Middle East region were deposited over a long geological time, from the Permian to the Paleocene, on an extensive shelf with minor disruption resulting in thick stacks of multiple carbonate pay-zones. Despite some geo-mechanical similarities along such an extensive area, it is important to recognize lithological variations, even within the same formations. Covering all the directional drilling would be beyond the scope of this article; consequently, some of the key directional drilling challenges to reach and drill these carbonate reservoirs will be discussed. As of Aug. 15, 2020, 54 wells have been drilled successfully in the Middle East with Magnus, utilizing its full commercialized suite of 11-in., 9 ½-in. and 6 ¾-in. sizes.
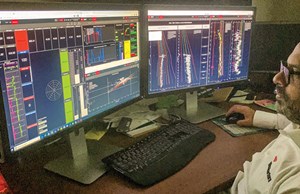
Formation interpretation and evaluation. One of the main successes of Magnus is to deploy LWD tools in the drilling BHA while maintaining high levels of service quality. This high reliability, coupled with excellent hole quality, have enabled multiple LWD runs, which typically would have required a dedicated wash down or wireline run to meet the formation evaluation objective. A particular success of Magnus has been zero stuck incidents, which has facilitated numerous radioactive runs or quad/penta combo LWD services. Furthermore, Magnus has landed and drilled a production section with full RT geo-steering service, including near-bit gamma ray, neutron-density, guidewave (azimuthal resistivity for optimum well placement), and sine-wave (high-resolution images to maximize production) in the same BHA. This well was ably supported by Weatherford’s Interpretation and Evaluation Services (IES) team, which helped the operator with answer products to address the high reservoir structural uncertainty.
Remote operations (RO). Most directional drilling service providers adopted remote operations several years ago, but the current Covid-19 pandemic makes them a necessity. Powered by Centro, Weatherford’s Drilling Services RTOC in Abu Dhabi supports RO in several Middle Eastern countries, ensuring job schedules are not impacted by personnel availability, and service quality levels are upheld at all times. This RTOC covers an average 14 RO jobs per week, enabling Weatherford to fully support its customers.
CONCLUSIONS
The advancements in directional drilling technology have significant impact on the life of the well, beyond drilling to the completions phase as well; this handshake between the service providers’ offerings and the customers’ objectives has been facilitated by adoption of digitalization and automation processes throughout all phases of the drilling engineering quality process: design, execute, evaluate and optimize.
While there are multiple RSS providers, only a few can offer comprehensive drilling solutions to operators globally, based on a wide range of tool sizes, operational reliability, seamless BHA integration, remote capability, global experience, and a sound drilling engineering quality process.